With industrial development, the demand for high-performance flocculants has been increasing. Polyacrylamide (PAM) has excellent flocculation properties and has been widely used in industries such as sewage treatment, papermaking, and mining. However, the solubility pattern of PAM in water directly affects its flocculation effect. Inappropriate solubilization methods not only reduce the utilization rate of PAM but also cause considerable economic burdens. Therefore, researching proper PAM solubility methods is essential for improving water treatment effects and reducing costs. Through this project, we aim to reveal the solubility mechanisms of PAM, identify the main factors affecting its solubility performance, propose efficient PAM solubilization techniques, and provide theoretical support for practical applications in production.
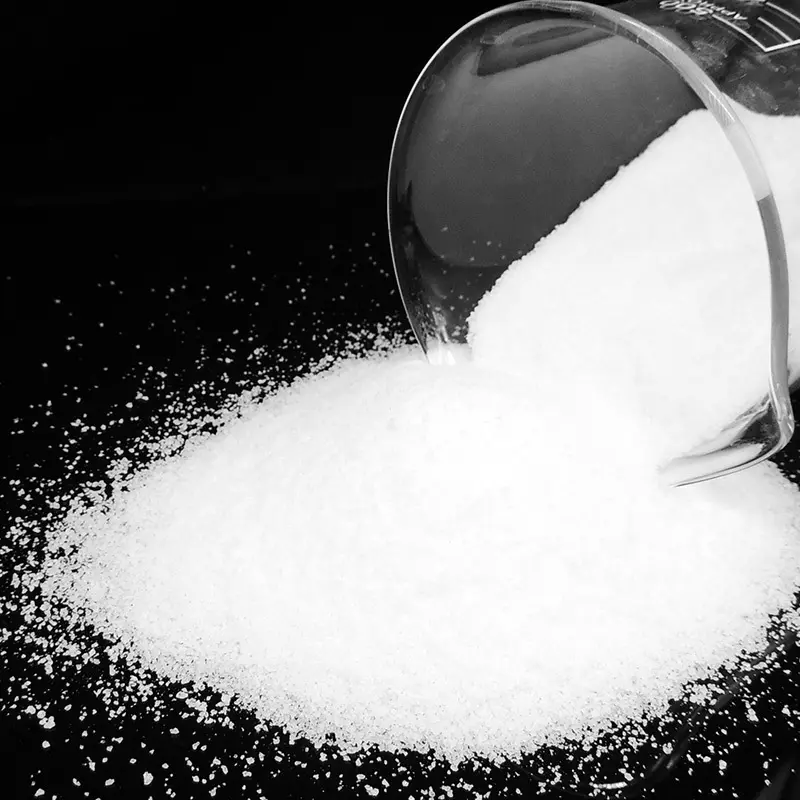
Specific steps for dissolving PAM are as follows:
- Polyacrylamide should not be added directly to water; it must be dissolved in water first, and then, according to the actual needs, its aqueous solution is added to the sewage for treatment.
- The water for dissolving polyacrylamide should not be wastewater, water with a high temperature, or water with strong acidity or alkalinity. Clean water, such as tap water, should be used.
- Our company suggests a solubility concentration of 0.1%-0.3% in the sewage treatment industry, which means 1-3 grams of polyacrylamide solid per liter of water. It is also possible to start dissolving at a slightly higher concentration and then dilute the flocculant mixture to the desired concentration before use.
- Polyacrylamide should be dispersed and dissolved carefully to avoid rapid dissolution on the powder surface, leading to inter-particle adhesion and the undissolved “fish eyes” within the particles. Therefore, various types of dispersing dissolvers are usually used.
- If not using a powder dispersing dissolver, the dissolution operation should proceed as follows:
- a) Fill the dissolution tank to half its volume with water.
- b) Stir with a mixer, allowing the measured polyacrylamide to be smoothly and evenly injected into the edge of the rotating vortex. The solution’s viscosity will increase after the polyacrylamide and solvent are fully mixed. Clumping may occur if the viscosity is too high. Continue stirring until the high molecular weight flocculant is completely dissolved.
- c) Stir in the same direction.d) The ideal mixing speed is 200-400 rpm. High-speed mixers are not recommended as they cannot reduce the motor’s speed, which would decrease the molecular weight of the flocculant. For a capacity of 1-2 cubic meters, the ideal mixer motor power should be 1 horsepower.
- Dissolution time. In summer, when water temperatures are higher, 40 minutes of stirring is sufficient for complete dissolution; in winter, with lower water temperatures, 1 hour of stirring is needed. Letting it sit for 1 to 2 hours after stirring for 40 minutes yields the best results.
- The equipment for preparing the solution should be made of stainless steel, fiberglass-reinforced plastic, or plastic-lined carbon steel to avoid contact between the solution and iron ions during preparation, storage, and transfer.
- Polyacrylamide can be stored for two years in a cool and dry environment. However, its aqueous solution has a limited effective storage time, so it is recommended to use it as soon as possible after preparation.
In-depth research on PAM indicates that rational dissolution is key to maximizing its flocculation effect. A good dissolution process can ensure that PAM achieves the best effect while reducing costs. In actual production, the dissolution process should be reasonably designed based on the molecular weight of PAM, concentration, dissolution time, and stirring rate.